- TOP
- 日本クリエイション大賞
- 授賞案件
- 日本クリエイション大賞2014 授賞案件
授賞案件
日本クリエイション大賞2014 授賞案件
大賞
四輪駆動で段差も乗り越える近未来型電動車いすを開発
WHILL(ウィル)株式会社
日本クリエイション賞
ケニア、ルワンダの人々の“自活”の道を切り拓いた日本の起業家
オーガニック・ソリューションズ 代表取締役社長 佐藤芳之氏
全国で唯一増収転換を果たした路線バス
十勝バス株式会社
常識を覆す不燃マグネシウムが世界の金属素材を変える
熊本大学先進マグネシウム国際研究センター センター長・教授 河村能人氏
2014年度選考について
日本クリエイション大賞2014 大賞
四輪駆動で段差も乗り越える近未来型電動車いすを開発
WHILL(ウィル)株式会社
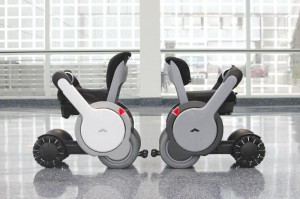
後輪部をすっぽり覆う白い円盤状のパーツが目を引く四輪のクールなデザインの乗り物。初めて目にする人は、車いすとは思わないかもしれない。
80年間ほとんど変化が起こらなかったと言われる車いすに、イノベーションを起こしたいとの意気込みで開発されたパーソナルモビリティー「WHILL Model A」の魅力は、そのデザイン性だけではない。前輪に24個の独立したタイヤからなるオムニホイールを採用した四輪駆動車で、最大7.5cmの段差を乗り越えることができる。芝生や砂利道、雪道などの悪路もスイスイ。オムニホイールは縦に回転するだけでなく、横方向にも転がるため、後輪を軸にして360度回ることもできる。日本の住居を考慮した小回り性能も抜群なのだ。
Bluetoothを内蔵し、iPhoneのアプリとも連動。本体が離れた場所にあってもiPhoneから遠隔操作で手元に呼び出すことが可能。また、最高速度や加速度もアプリを使って走行設定できる。なお、充電は家庭用電源ででき、1回あたり5時間の充電で20kmの走行が可能という。価格は95万円だが、2014年9月、日米で50台の限定生産を発表したところ、国内外から多くの引き合いがあり、即完売したというのもうなずける。
このまさしく近未来型の電動車いすを開発したのは、2012年創業のベンチャー企業WHILL(ウィル)株式会社。日本の有名メーカーを飛び出した若手デザイナーとエンジニアが立ち上げた。日本だけで考えると電動車いすの市場は狭いが、アメリカには日本の約15倍、17億ドルの市場があると言われ、資金集めにも有利なことから、企画およびマーケティングの拠点としての本社を、米・シリコンバレーに置く。日本は開発拠点と位置付け、生産は台湾で行い、低コストで安定したオペレーション体制を整えている。2015年度には、台湾で2,000台の生産を予定し、世界での販売を見込んでいる。
シリコンバレーの有力ベンチャーキャピタル「500Startups」からの出資を受け、これを弾みに日米、台湾から総額1,100万ドルの資金調達を実現。日本の高い開発力を活かして、創業当初から世界をマーケットにものづくりを行う、ベンチャーのモデルのようなプロジェクトだ。
日本の若い力が、電動車いすのみならずパーソナルモビリティーの世界を変えようとしている。
日本クリエイション大賞2014 日本クリエイション賞
ケニア、ルワンダの人々の“自活”の道を切り拓いた日本の起業家
オーガニック・ソリューションズ 代表取締役社長 佐藤芳之氏(ケニア・ナッツ・カンパニー創業者)
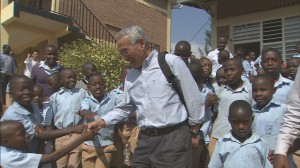
1939年生まれの佐藤芳之さんは、高校時代に、ホームルームで10年後自分がどこで何をしているかを発表したとき、「僕はアフリカにいます」と宣言した。
1963年、佐藤さんはその言葉どおり、東京外国語大学を卒業後、アフリカ独立の父、クワメ・エンクルマに憧れて、日本人初の留学生としてガーナ大学で学ぶ。修了後、ケニアで東レ・ミルズに現地職員として入社。退職後、一時帰国をしたものの32歳で単身ケニアに戻り、鉛筆工場、製材工場、ビニールシート工場など小規模なビジネスを次々と立ち上げ、1974年「ケニア・ナッツ・カンパニー」を創業。
「アウト・オブ・アフリカ」というマカダミアナッツのオリジナル・ブランドをヒットさせ、同社を年商30億円の世界5大マカダミアナッツ・カンパニーにまで育てあげる。2008年、延べ10万人におよぶケニア人の雇用を生み出したこの会社をただ同然で手放し、ケニア人パートナーの手に委ねる。もともとケニアの人々の自活の道を切り拓くために、ケニア人のためになることをしたいと立ち上げた会社だったからだ。
70歳を目前にした佐藤さんは、2005年から立ち上げていた微生物ビジネスの会社「オーガニック・ソリューションズ」で、くみ取り式のトイレが中心で、衛生上の問題を抱えるアフリカで微生物を使った汚水処理事業に本格的に取り組み、内戦からの復興を遂げつつあるルワンダで、微生物資材を製造販売する会社オーガニック・ソリューションズ・ルワンダを創業。小売店網が発達していない同国で、保健省の環境衛生官やコミュニティヘルスワーカーを通じて、全国に流通させる努力を続けている。わずか5分程度で強烈なにおいが消えるこの資材は、ルワンダの3,000余の学校のうち、既に1,000校で採用されているという。
人生は「やるか、やらないか」だと語る佐藤さんは、やりたいことは常に言葉にし、高校時代の宣言どおり75歳の今もアフリカの大地に立って、アフリカの人々のためのビジネスを続けている。
佐藤さんのアフリカでの40年に及ぶ歩みと思いは、著書の「OUTOF AFRICA アフリカの奇跡」(朝日新聞出版/2013年)「歩き続ければ 大丈夫」(ダイヤモンド社出版/2014年)に綴られている。
全国で唯一増収転換を果たした路線バス
十勝バス株式会社
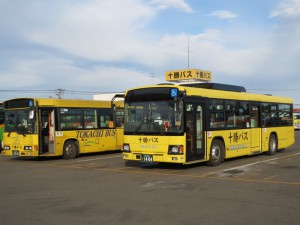
北海道の帯広市を中心に十勝地方全域で、市民の足として愛されてきた十勝バスだが、全国の他の路線バスと同様、人口減やマイカーブームなどによって利用者がピーク時から約8割減、20年間で営業収益も半減、2008年には世界的な原油価格の高騰もあって、銀行からも融資を断られ倒産寸前という事態に陥っていた。
2003年、父・野村文彦氏から39歳の若さで会社を引き継いだ野村文吾社長は、利用者減少を「自然減」と認識していた社員に対し、自ら歩み寄り、一人ひとりに自分の思いを語っていった。すると、社員の中から周辺住宅を一軒一軒訪ね、住民から直接路線バスについての意見を聞いて回ろうという「御用聞き活動」のアイデアが出る。それを実践したところ、「不便だから」バスに乗らないのではなく、多くの人々がバスに乗る際のさまざまな「不安」からバスを敬遠していることを知り、その不安や不便を社員で話し合い改善を図る。
町内会の体験乗車会の実施など、バスの乗り方から丁寧に説明し、エリアを絞った通院や買い物などの目的別時刻表、沿線の見学施設や商業施設までの往復乗車券と施設利用料とがセットになった日帰り路線バスパック、通勤通学定期で土日祝日帯広市内全域乗り放題、高校スクールバス部活便の運行など新しいサービスを次々と打ち出し、乗客にとって魅力的なバスの乗り方を提案していった結果、平成23年度、路線バス会社としては全国で唯一増収増益を果たす。十勝バスとしても40年ぶりの増収転換だった。平成24年度、25年度も3年連続で前年実績を上回っている。
十勝バスの変化は業績が改善しただけではない。社員のアイデアから生まれた企画を次々と形にしていったことに対し、お客様から感謝の声が届くようになり、社員が自信と誇りをもって現場に出るようになった。社員同士、またお客様との間に対話と笑顔が増え、守りの意識が強かった社風が、明るく前向きなものに大きく変わったという。
十勝バスは、路線バスという単なる移動手段を提供する会社から「目的提案企業」になろうと、野村社長を先頭に全社員が今日も努力を続けている。
常識を覆す不燃マグネシウムが世界の金属素材を変える
熊本大学先進マグネシウム国際研究センター センター長・教授 河村能人氏
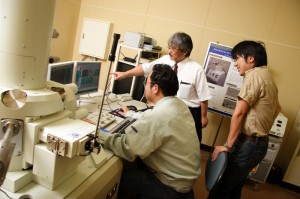
マグネシウムは実用金属の中で最も軽く、海水中に含まれるなど資源量も豊富な一方で、強度が低く熱に弱い。そのため、パソコンや携帯電話など、用途が限られていた。そこで、ほかの金属と混ぜる合金として、強度や耐熱性、発火温度を上げようと、世界各国が開発を競ってきた。
熊本大学の河村能人教授がマグネシウム研究を始めたのは、1999年。既にその研究はやり尽くされたと考えられていた。それでも河村教授は、一種類ずつ金属を混ぜ強度を測るという地道な作業を繰り返し、1%単位で配合率を変えながら、検証を続けていった。
そうしてたどり着いた『KUMADAI 不燃マグネシウム合金』は、1,117度でも発火しない、世界初の不燃マグネシウム合金である。航空機などに使われるジュラルミンより軽く、強度は1.4倍。これまでマグネシウム合金は発火しやすいという理由で、民間航空機への使用が禁止されていたが、「KUMADAI 不燃マグネシウム合金」は米連邦航空局(FAA)の燃焼試験に合格。従来の難燃性マグネシウム合金等と比べ、低コストでの生産が可能で、リサイクルもできるため、航空機の機体や高速鉄道車両、船舶、自動車等の新素材として、世界の産業界から注目されている。
熊本大学は、2011年に不燃マグネシウム合金の研究開発と本格実用化を目指して、構内に「熊本大学先進マグネシウム国際研究センター」(MRC)を設立した。2014年には、熊本大学と世界最大の航空機メーカーである米ボーイング社が、「KUMADAI 超急冷耐熱マグネシウム合金」の航空機への応用に向けて、共同研究の協定を締結。2020年にボーイングが始める次世代航空機開発への採用を目指す。超急冷法によって金属組織が微細で均一になり、鋳造で製作する場合と比べて、強度で1.6倍、耐食性で10倍になるという。
2015年には日本の素材や機体のメーカーが参加し、航空機の骨格部品などに使える大型素材の低コスト量産技術の開発に取り組む予定である。これによって、航空機用マグネシウム合金素材のサプライチェーンを構築することができ、日本の航空機産業の発展に大きく貢献できるものと期待されている。